
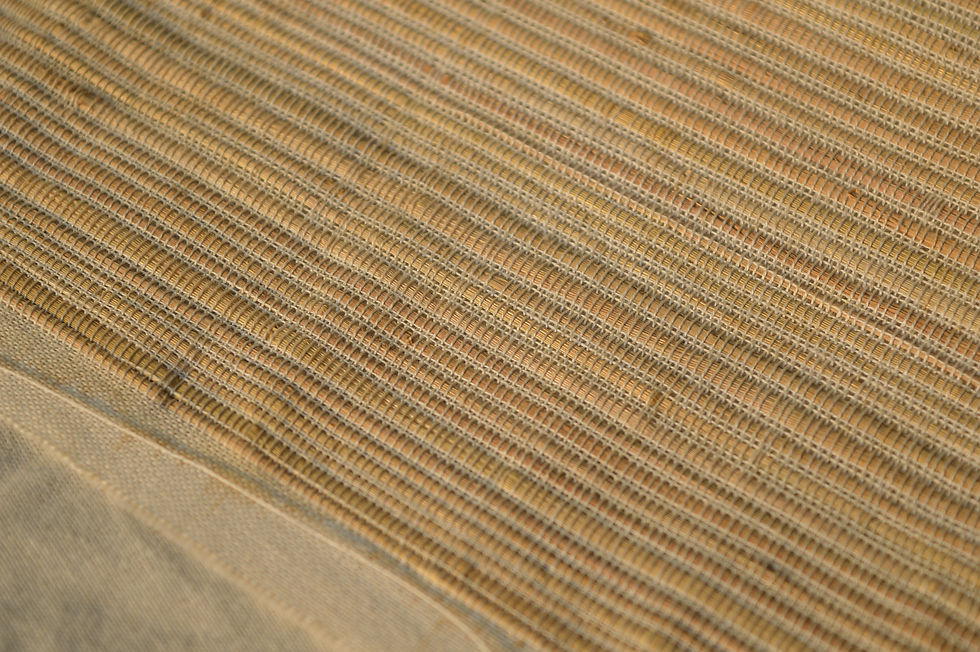

NEED BASED TRANFORMATION
Guided by Ram Mattegunta
The objective of the Need based transformation course was to analyze various systems and identify areas requiring design interventions. By using textile and design knowledge , we sought to develop sustainable solutions to address these needs effectively.
Additionally, during the course, the pressing need for managing rice straw left after cultivation was recognized. As a result, efforts were made to explore ways to repurpose rice straw for useful applications. This underscored the importance of seeking innovative approaches to mitigate agricultural waste while simultaneously creating value from otherwise unused resources.

Located in a small village surrounded by farms, the college witnessed daily truckloads of straw passing by, prompting a curious observation. Upon delving deeper, it was discovered that Andhra Pradesh ranked as the third-largest producer of rice, thereby generating significant quantities of straw.
Subsequent research revealed a prevalent issue of rice straw burning in northern India, contributing substantially to poor air quality in the region. Shockingly, out of the 26 million tons of straw produced annually in India, a staggering 60 percent is burnt, aggravating environmental concerns.

RICE STRAW
Rice straw is the vegetative part of the rice plant, cut at grain harvest or after. Ratio of straw to paddy ranges from 0.7-1.4 depending on the variety and growth. Rice straw contains 38% cellulose, 25% hemicellulose, and 12% lignin.
Rice straw is used for -
- Livestock bedding and Fodder.
- Building material
- Packaging
- Heating fuel
NEED FOR INTERVENTION
In traditional Asian practices, rice is typically harvested manually, where it's cut and transported to a central threshing area for separating grain and straw. In this process, only a small portion of straw is typically left in the field. However, the growing utilization of combine harvesters has led to significant amounts of rice straw being left behind in the fields. This excess straw is either incorporated back into the soil through ploughing or disposed of through burning.

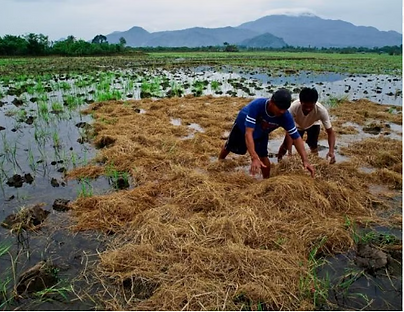
RICE STRAW INCORPORATION
Incorporating rice straw is labor-intensive and affects greenhouse gas emissions but can enrich soil organic carbon and recycle nutrients. Properly managed, it maintains soil fertility. However, poor management can reduce efficiency and increase emissions. Slow decomposition often deters farmers from incorporating crop residues. Excess straw poses challenges, requiring mechanization and multiple tillage for effective soil incorporation.
​
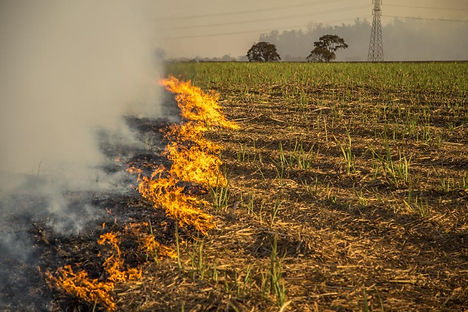
BURNING
​
Straw burning releases particulate matter into the atmosphere, which is associated with air pollution and human respiratory ailments.
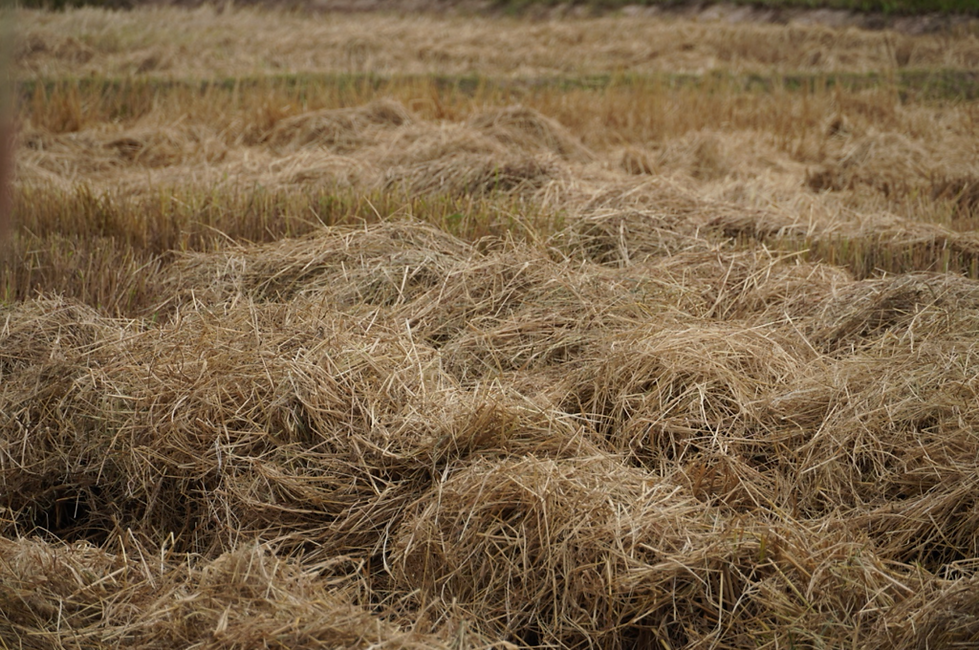
POSSIBLE WAYS OF INTERVENTION
Processing the straw into paper.
Exploring with different textile techniques like weaving, trying out different weaves and
weaving techniques. And looking into the possible ways of introducing it into the system.
PAPER MAKING PROCESS
The production process of the paper that we use is highly energy and water intensive. Wood undergoes sulphate treatment and bleaching, involving chemicals such as sodium hydroxide(caustic soda), sodium sulphide, and hydrogen peroxide, which leave significant environmental footprints. These chemicals are costly and entail additional expenses for transportation. As an alternative, efforts were made to explore greener methods, such as substituting of caustic soda with a weaker version i.e baking soda.

The paper making process starts with soaking the paddy straw in water overnight.
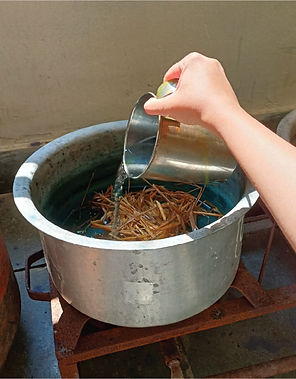
Transfer the straw in a container and add water untilit is completely submerged.

Chemical treatment: Add the chemicals based on the volume of water used.

Let it boil for 2-3 hours, till the straw disintegrates.

In a big tub pour the slurry
and enough of water
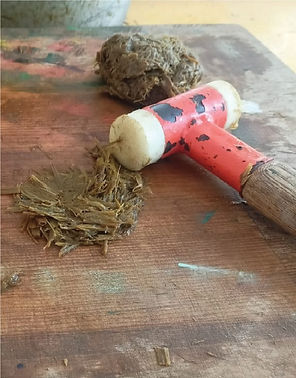
Beat it , for the fibers to soften a bit.
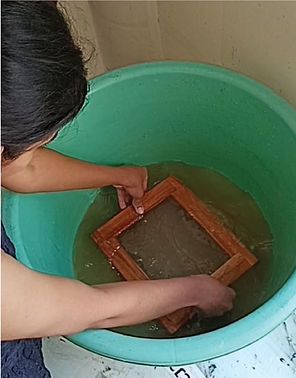
Put the paper making mesh inside the water and try creating a even surface with fibers over the mesh. Then put it over a wet fabric.

Wash it thoroughly with water
few times and grind it. Then the slurry is ready.

Dab the excess water out with the help of a dry fabric and lift the mesh so that the fibres are deposited on the fabric properly.

Put it for drying.

Carefully take the paper out by stretching the fabric.



WOVEN SAMPLES AND PRODUCTS DEVELOPED WITH IT.
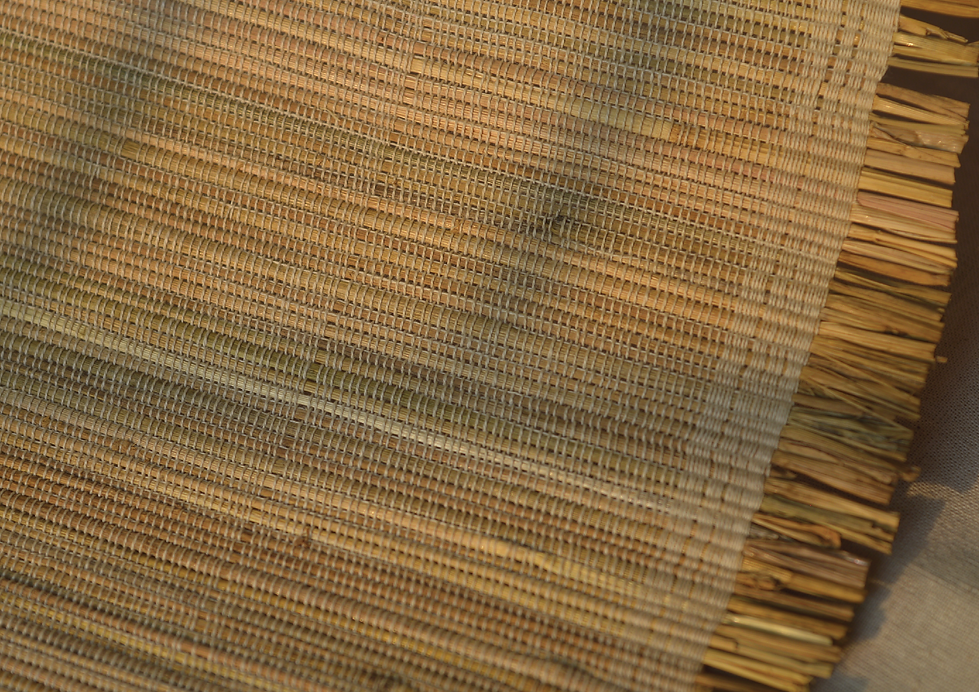




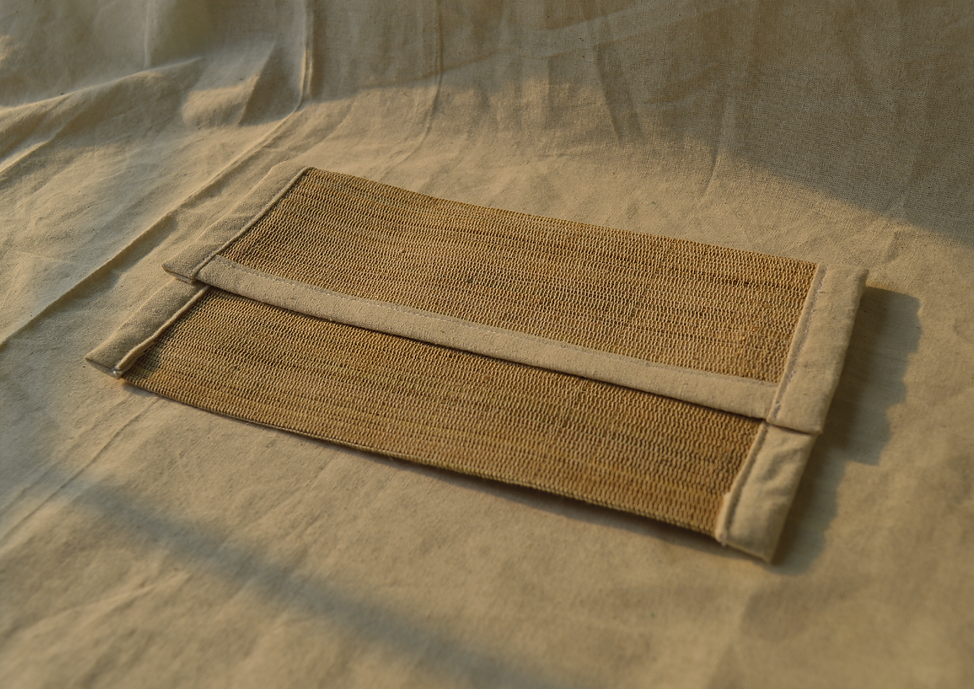
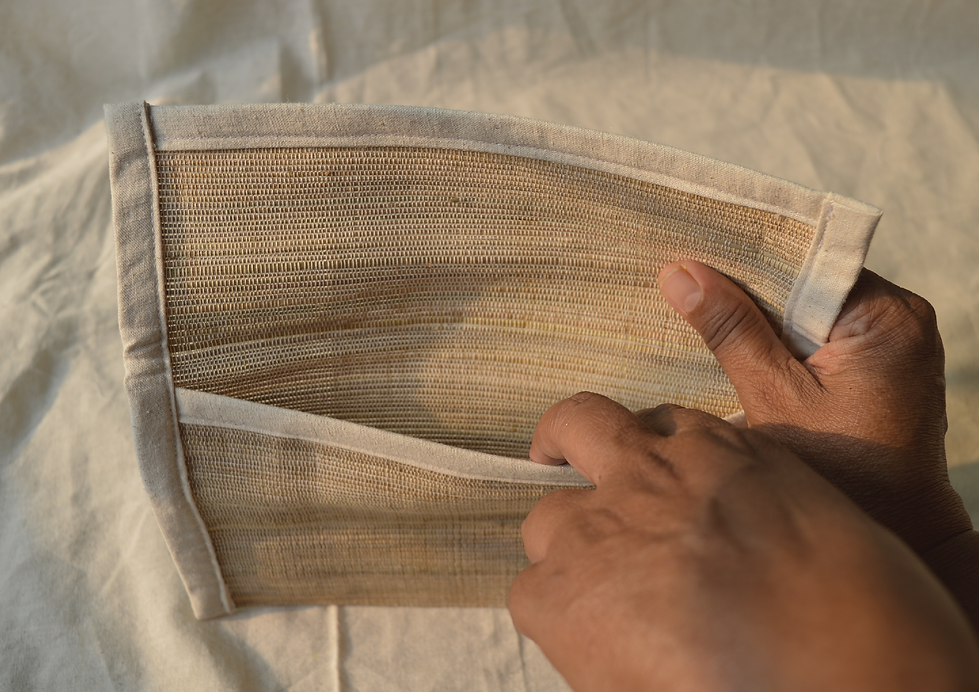

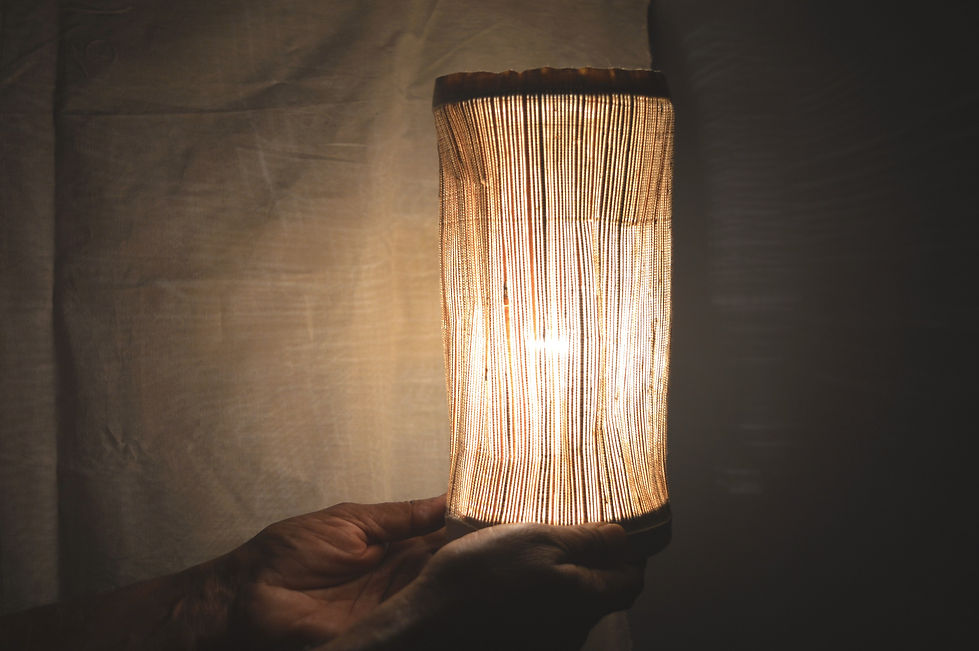